La fabrication d’une carte électronique est un processus complexe, précis et rigoureux impliquant plusieurs étapes clés pour garantir la fonctionnalité et la fiabilité du produit final comprenant : la préparation des composants, la sérigraphie, le placement automatisé des composants CMS, la soudure par refusion puis des contrôles qualité visuels et automatisés.
Les étapes de fabrication de cartes électroniques en vidéo.
- La sécurité au cœur de la fabrication des cartes électroniques
- Gestion et préparation des composants et des PCB
- La sérigraphie du PCB : préparer le circuit à recevoir les composants
- Le placement automatique des composants CMS
- Soudure et contrôle qualité
- Quels sont les points clés à retenir ?
- Pourquoi faire appel à TEC Électronique pour la fabrication de vos cartes électroniques ?
La sécurité au cœur de la fabrication des cartes électroniques
La sécurité est une priorité absolue dans la fabrication d’une carte électronique, tant pour protéger les personnes que pour garantir l’intégrité des composants. Les cartes électroniques intègrent des composants sensibles aux variations électriques et aux conditions environnementales.
L’un des risques majeurs en atelier de pose CMS est la décharge électrostatique (ESD), invisible à l’œil nu, mais capable d’endommager ou de dégrader un composant avant même qu’il soit installé. Pour limiter ce risque, des mesures strictes sont mises en place dès l’entrée en zone de production : port obligatoire de blouses ESD, talonnettes antistatiques et respect de protocoles précis.
Au-delà de l’ESD, la sécurité dans la fabrication couvre également la gestion des risques électriques, thermiques, chimiques ou mécaniques liés aux processus industriels (soudure, découpe, test, etc.). Le respect des normes de qualité et des procédures de contrôle permet de s’assurer que chaque carte électronique fonctionne de manière fiable, durable et sécurisée, notamment dans des domaines critiques comme la santé ou l’aéronautique.
Gestion et préparation des composants et des PCB
La gestion des composants électroniques et des cartes de circuits imprimés (PCB) est un maillon essentiel du processus de fabrication. Tout débute au magasin, véritable cœur logistique de l’atelier, où sont stockées des milliers de références soigneusement classées. Ce lieu centralise l’ensemble des éléments nécessaires à l’assemblage des cartes, assurant à la fois disponibilité, traçabilité et réactivité.
Avant toute opération de production, les techniciens rassemblent les composants et les PCB requis, selon la nomenclature définis. Chaque référence est identifiée avec précision, ce qui permet de suivre son utilisation à chaque étape.
Grâce à une organisation rigoureuse, la production est alignée en temps réel avec les besoins des clients, en assurant la qualité, les délais et la cohérence des lots produits.
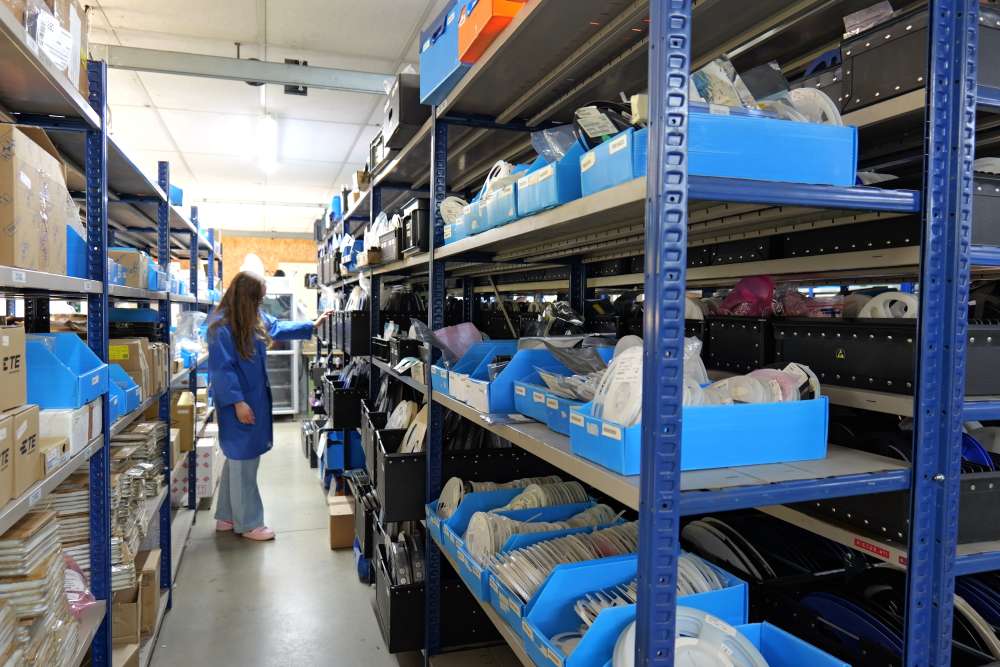
La sérigraphie du PCB : préparer le circuit à recevoir les composants
Une fois les composants rassemblés et le PCB récupéré depuis le magasin, l’étape suivante du processus de fabrication consiste à sérigraphier le circuit imprimé pour y déposer la pâte à braser. Cette opération est réalisée à l’aide d’un pochoir métallique sur mesure, installé dans une machine de sérigraphie. Le pochoir, fabriqué à partir des fichiers techniques de la carte, délimite avec précision les zones du PCB où la pâte doit être appliquée.
La pâte à braser est ensuite déposée sur le circuit à travers le pochoir. Elle joue un double rôle : maintenir temporairement les composants sur la carte et permettre, lors de la refusion, la formation de connexions électriques solides entre les composants et les pistes du PCB.
Selon les cas, le pochoir peut être fourni directement par le client ou conçu dans le cadre d’un projet de co-conception. Sa précision est déterminante : une mauvaise application de la pâte à braser peut entrainer des défauts critiques comme des courts-circuits ou des soudures froides. C’est pourquoi cette étape, bien que rapide, fait l’objet de contrôles rigoureux dans le cadre d’un processus global sécurisé, assurant la qualité et la fiabilité des cartes électroniques produites.
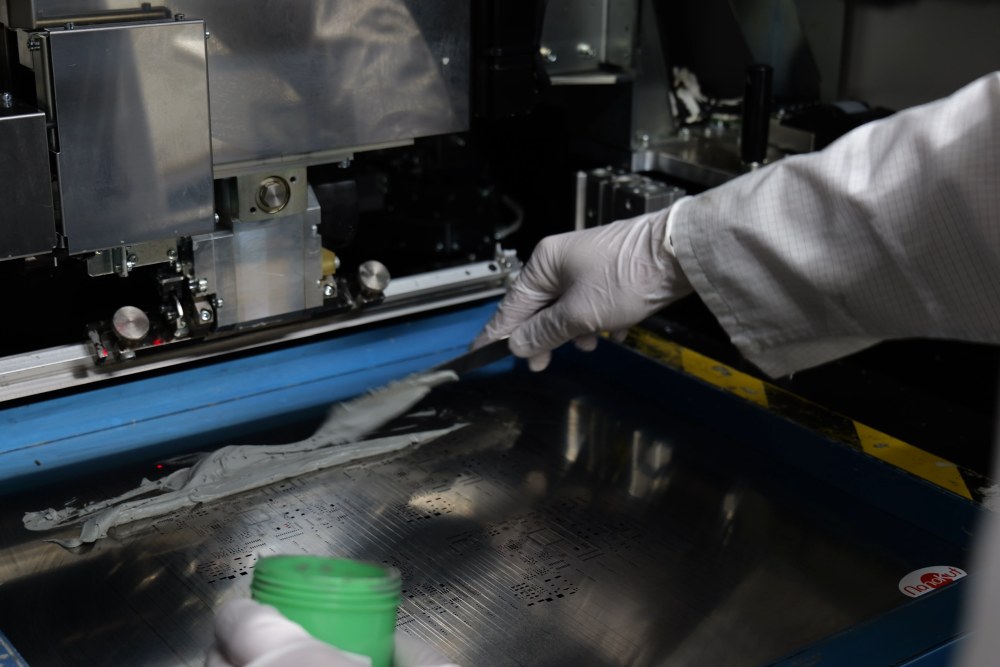
Le placement automatique des composants CMS
Une fois la sérigraphie du PCB réalisée et la pâte à braser déposée avec précision, l’étape suivante consiste à positionner automatiquement les composants CMS (Composants Montés en Surface) sur la carte.
Cette opération est assurée par une machine de pose CMS, programmée spécifiquement pour chaque modèle de carte électronique. Le fichier de placement chargé dans la machine contient toutes les informations nécessaires :
- le plan de chargement,
- les coordonnées précises des composants
- l’emplacement de chaque bobine de composants, identifiées par un code unique.
Le processus commence par une phase d’apprentissage, la machine pose d’abord les composants un par un, pour calibrer précisément ses gestes mécaniques. Puis, elle monte progressivement en cadence, jusqu’à déposer les composants par groupe de 4, 8, voire 16, tout en assurant un fonctionnement fluide grâce à un double bras automatisé. Tandis que l’un dépose les composants, l’autre prépare les suivants.
Un système de contrôle intégré permet de détecter immédiatement les erreurs de positionnement ou les absences de composants. En cas de problème repéré sur une même bobine, la machine met automatiquement le couloir concerné en pause et alerte le technicien, qui peut alors intervenir. Cette phase de réglage est particulièrement importante lors du premier passage d’une nouvelle carte, qui constitue toujours un test en conditions réelles. Les réglages peuvent alors être affinés avant le lancement en série.
Dans notre exemple dans la vidéo ci-dessus, la machine place avec précision 1400 composants sur chaque carte.
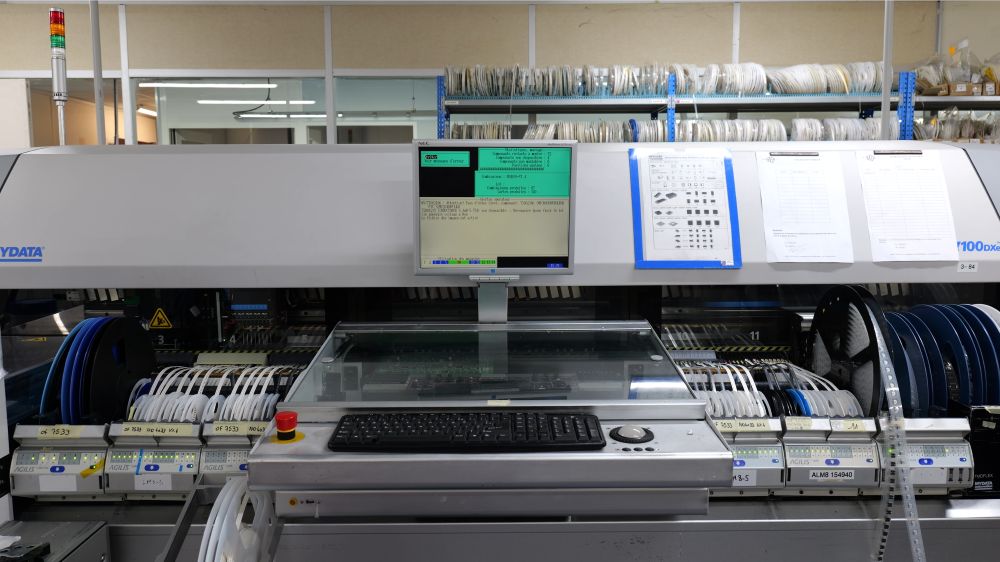
Soudure et contrôle qualité
Après la sérigraphie du PCB et le placement automatique des composants CMS, chaque carte passe par une étape essentielle : le contrôle visuel manuel, réalisé avant son passage au four à refusion. Cette vérification rapide mais rigoureuse permet d’anticiper d’éventuels défauts qui pourraient compromettre la soudure ou nécessiter des retouches coûteuses par la suite.
Un contrôle visuel indispensable avant la soudure
Avant même le passage au four à refusion, chaque carte fait l’objet d’un contrôle visuel manuel. Cette étape permet de détecter en amont les erreurs susceptibles d’affecter la qualité de la soudure.
Les techniciens comparent la carte produite à une référence fournie par le client ou validée en interne. Ils vérifient notamment :
- la présence de tous les composants,
- leur orientation correcte, en particulier pour les composants polarisés,
- la valeur apparente de certains composants, lorsque celle-ci est identifiable visuellement,
- l’alignement précis sur les pastilles.
Ce contrôle dure en moyenne deux minutes par carte, et permet de détecter rapidement des défauts comme :
- un composant manquant,
- une pièce inversée,
- un mauvais positionnement.
L’objectif de ce contrôle est d’éviter des retouches coûteuses après soudure.
Le rôle du four à refusion
Une fois validées, les cartes sont dirigées vers le four à refusion, où la pâte à braser fond sous l’effet de la chaleur. Ce processus permet de :
- fixer définitivement les composants,
- créer des connexions électriques solides entre les broches et les pistes du PCB.
Les paramètres du four sont rigoureusement contrôlés :
- température adaptée à l’alliage utilisé,
- courbe de chauffe précise pour éviter les chocs thermiques,
- refroidissement maîtrisé pour stabiliser les soudures.
L’objectif est de garantir des soudures fiables, sans défauts d’alliage ni surchauffe.
Inspection finale par AOI
Après la refusion, chaque carte est soumise à une inspection optique automatisée (AOI). Cette machine utilise des caméras haute résolution et de l’intelligence embarquée pour vérifier :
- le positionnement exact des composants,
- les références des composants via lecture OCR (reconnaissance optique de caractères),
- la qualité des soudures : détection de ponts, soudures froides, absences de brasure…
Grâce à l’AOI, la plupart des défauts sont identifiés sans intervention humaine, avec une grande rapidité et fiabilité.
Pourquoi un contrôle visuel humain reste-t-il nécessaire ?
Malgré la précision des machines, certaines vérifications restent confiées à des opérateurs expérimentés. Leur œil peut détecter des éléments que l’AOI pourrait ignorer, notamment :
- des microfissures,
- des défauts d’aspect ou d’alignement subtils,
- des incohérences visuelles qui ne correspondent pas aux critères strictement techniques mais relèvent du savoir-faire métier.
Ce double regard humain et machine, garantit un niveau de qualité optimal avant l’étape suivante : l’intégration ou le test fonctionnel.
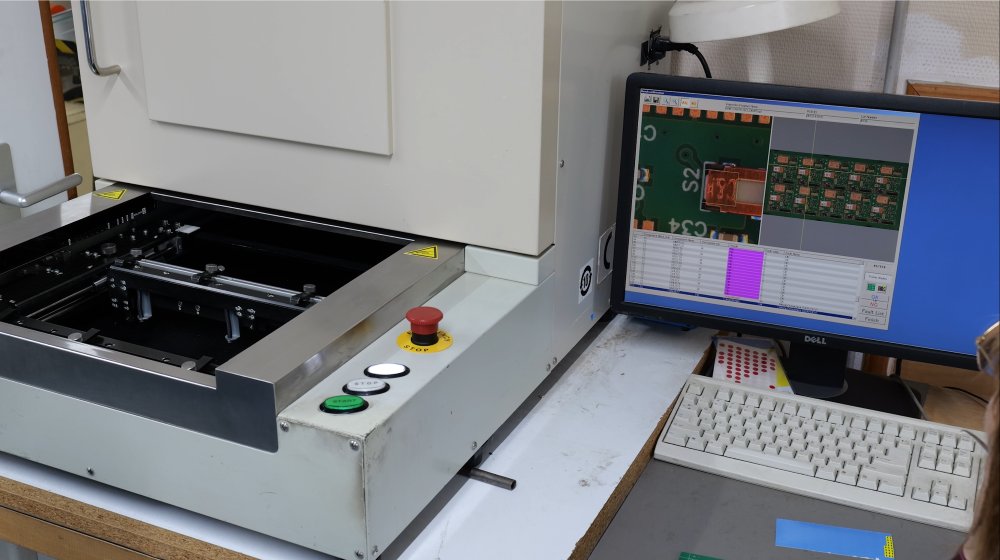
Quels sont les points clés à retenir ?
La fabrication d’une carte électronique est un processus hautement technique, automatisé et sécurisé. Chaque étape, de la préparation des composants à l’inspection finale contribue à garantir la fiabilité, la performance et la conformité des produits livrés aux clients. Grâce à une combinaison d’automatisation avancée, de contrôles qualité rigoureux et d’une gestion précise des flux de production, Groupe TEC est en mesure de produire des cartes électroniques complexes avec une grande efficacité.
Pourquoi faire appel à TEC Électronique pour la fabrication de vos cartes électroniques ?
Contactez notre équipe expertes pour vous accompagner dans votre projet, de la conception au test final. Notre expertise en assemblage CMS, nos équipements techniques et notre rigueur qualité sont à votre service.
Prenez contact avec nous dès maintenant